Due to my long absence my previous thread was archived so I'll start a new one here.
My first task was to get the new compressor installed and the air system plumbed in. I have to say I love this new compressor! My air supply is as reliable and consistent as my electricity now.
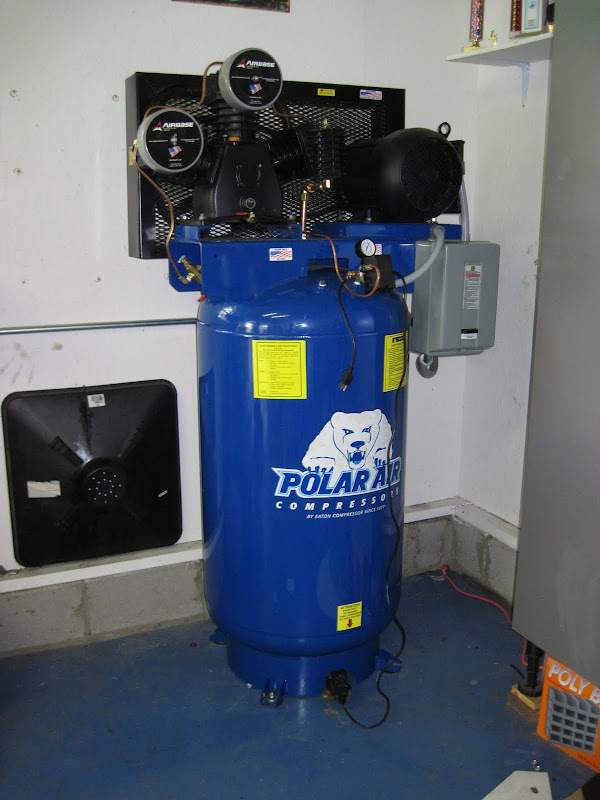
I picked up a few parts during my trip, not everything I was hoping to find but I'll take what I can get. The biggest is a centered rear axle housing which I'll swap out when I start the axle restoration. The other was a new gas tank. A 40 gallon unit Chris Case is building from Stainless setup for diesel. I also managed to get some rear shock mount brackets to go with that centered axle housing when I swap it out.
The work blasting and prepping parts continues, I'm going to need to start playing with my spray gun as lots of the stuff I'm working with now will get painted to match the frame or body vice powder coated.
However I did order one of the Ugly Truckling power steering conversion brackets and a reverse rotation box from AGR performance.
The box is built very nice with some upgrades and improvements, including slightly firmer valving and billet end caps. Installation requires some modifications to the frame however.
First I fit the bracket to the stock location without the box to make sure it bolted up properly. You have to make sure the frame surfaces are clean since the bracket sits flat against the inside of the frame rail and is larger than the flange of the stock steering box. Then four supplied bolts thread into the plate through the stock holes. I had some issues with one of the bolts but some minor dremel work on one of the frame holes created the extra space I needed.
Once I got the new steering box I bolted it to the adapter, which also had some interference issues. One of the round spacers provided has a side ground into it to clear the side of the adapter plate. The boss on the steering box was too thick and would not line up with that hole so a little metal removal was required there too. I don't love grinding on a fresh box but it's preferable to grinding on the bracket since that would compromise the strength where the metal removed from the box is not as structurally important.
Then it was time to fit it to the frame. This requires clearancing the top of the frame C-channel to fit around the box. The instructions provided discuss what to cut and grind. The key is lots of fitting and a little bit of grinding.
I would hold the assembly into the frame and mark out where it was hitting. Do a little grinding, cutting, and/or bending, then re-fit the bracket and see where the new interference was. Very tedious but the cut-out ends up being very close for a clean look, and it reduces the material removed from the frame.
The bracket is very beefy so I think it easily helps compensate for the metal removed from the frame, and it's held in with heavy duty fine-thread bolts.
With enough material removed I bolted up the box and checked the fit. The pitman shaft looked to be just touching the lower side of the hole so I opened it up slightly with the dremel to make sure there was no rubbing. Then I test fit the pitman arm to make sure everything worked. I didn't torque the pitman arm bolt (or any of the others for that matter) since I'm going to re-install the manual box to allow me to move the frame around more easily.
My only concern is that the arm of the new box isn't as long as the manual one, so the pitman arm will have to sit much closer to the frame in order to get a good engagement. It should be fine, there appears to be enough clearance between the bracket bolts and the arm to allow me to get good engagement of the arm to the box.
Next I'll be working on that 3rd cross member that's rusted out. I have some sheet metal being fabbed to install that will be cleaner and stronger than welding it all from flat pieces.
It's nice to be home working in the garage, now if only I could have brought the San Diego weather home with me. 100 degree temps don't encourage outdoor work.
My first task was to get the new compressor installed and the air system plumbed in. I have to say I love this new compressor! My air supply is as reliable and consistent as my electricity now.
I picked up a few parts during my trip, not everything I was hoping to find but I'll take what I can get. The biggest is a centered rear axle housing which I'll swap out when I start the axle restoration. The other was a new gas tank. A 40 gallon unit Chris Case is building from Stainless setup for diesel. I also managed to get some rear shock mount brackets to go with that centered axle housing when I swap it out.
The work blasting and prepping parts continues, I'm going to need to start playing with my spray gun as lots of the stuff I'm working with now will get painted to match the frame or body vice powder coated.
However I did order one of the Ugly Truckling power steering conversion brackets and a reverse rotation box from AGR performance.
The box is built very nice with some upgrades and improvements, including slightly firmer valving and billet end caps. Installation requires some modifications to the frame however.
First I fit the bracket to the stock location without the box to make sure it bolted up properly. You have to make sure the frame surfaces are clean since the bracket sits flat against the inside of the frame rail and is larger than the flange of the stock steering box. Then four supplied bolts thread into the plate through the stock holes. I had some issues with one of the bolts but some minor dremel work on one of the frame holes created the extra space I needed.
Once I got the new steering box I bolted it to the adapter, which also had some interference issues. One of the round spacers provided has a side ground into it to clear the side of the adapter plate. The boss on the steering box was too thick and would not line up with that hole so a little metal removal was required there too. I don't love grinding on a fresh box but it's preferable to grinding on the bracket since that would compromise the strength where the metal removed from the box is not as structurally important.
Then it was time to fit it to the frame. This requires clearancing the top of the frame C-channel to fit around the box. The instructions provided discuss what to cut and grind. The key is lots of fitting and a little bit of grinding.
I would hold the assembly into the frame and mark out where it was hitting. Do a little grinding, cutting, and/or bending, then re-fit the bracket and see where the new interference was. Very tedious but the cut-out ends up being very close for a clean look, and it reduces the material removed from the frame.
The bracket is very beefy so I think it easily helps compensate for the metal removed from the frame, and it's held in with heavy duty fine-thread bolts.
With enough material removed I bolted up the box and checked the fit. The pitman shaft looked to be just touching the lower side of the hole so I opened it up slightly with the dremel to make sure there was no rubbing. Then I test fit the pitman arm to make sure everything worked. I didn't torque the pitman arm bolt (or any of the others for that matter) since I'm going to re-install the manual box to allow me to move the frame around more easily.
My only concern is that the arm of the new box isn't as long as the manual one, so the pitman arm will have to sit much closer to the frame in order to get a good engagement. It should be fine, there appears to be enough clearance between the bracket bolts and the arm to allow me to get good engagement of the arm to the box.
Next I'll be working on that 3rd cross member that's rusted out. I have some sheet metal being fabbed to install that will be cleaner and stronger than welding it all from flat pieces.
It's nice to be home working in the garage, now if only I could have brought the San Diego weather home with me. 100 degree temps don't encourage outdoor work.
Comment