Wondering if you all weld in or fill seams when doing extensive body work on the cab? Here are a few pics of my cab that has been media blasted and primed. I'm wanting to fill the seam across the roof and cut out the drip edge above the door (not sure if it's a good idea but I like the clean look). Also wondering if I should spend some time filling the various seams on the floor around the door.
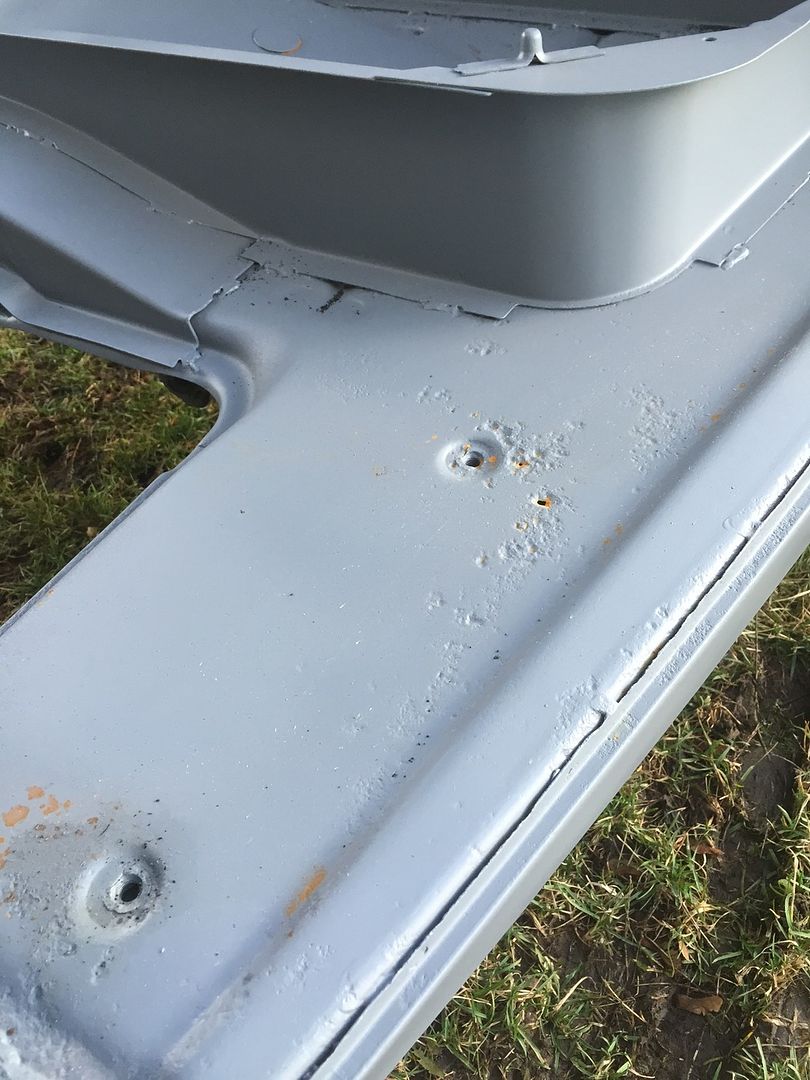
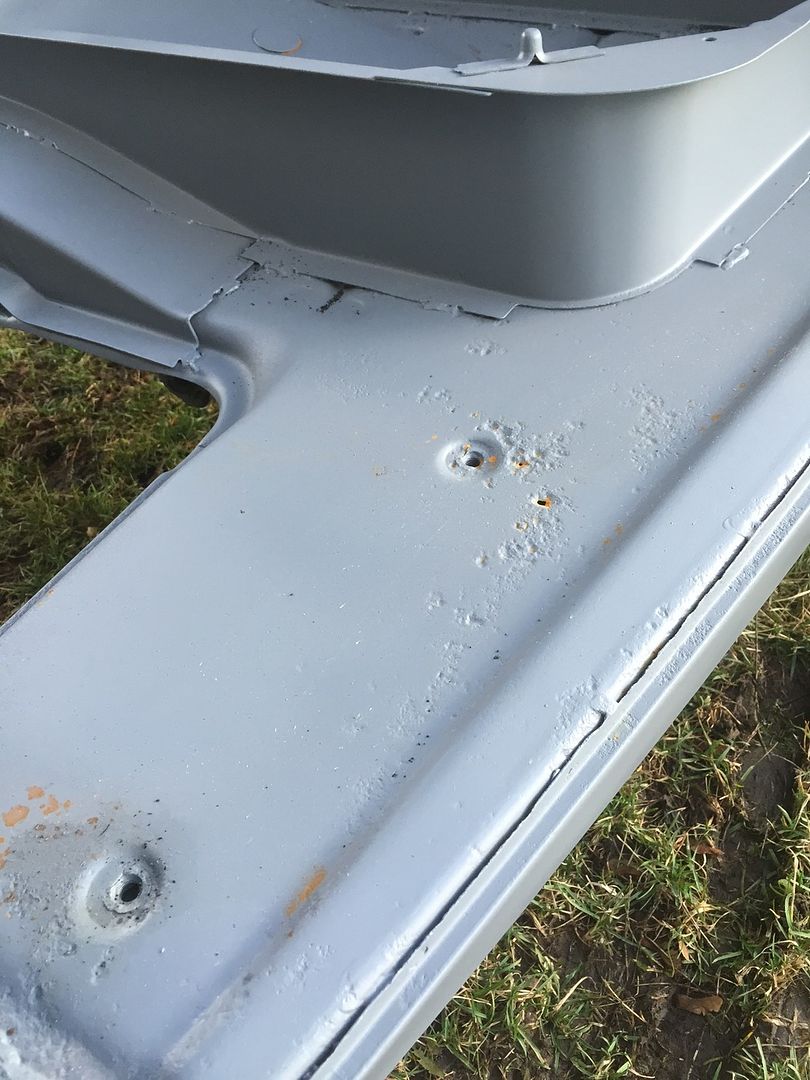

Comment